Specialty Materials
Products
metallic honeycomb manufacture
Magellan designs and manufactures metallic laser welded and resistance welded honeycomb using stable and repeatable processes and has unique attributes for higher temperature applications where glued honeycomb structures cannot perform. The products are typically produced in materials suitable for higher temperatures such as titanium, Inconel, stainless steel, and exotic alloys where strength and temperature are both key design considerations.
The key technological advantages of laser welded honeycomb include weight savings, higher node strength, and a wide range of design flexibility including aluminum laser welded honeycomb.
Honeycomb can be produced with many different controllable features, including:
Type
- Expanded core
- Variable cell honeycomb
- Perforated
- Slotted
- Energy absorbing
- Angled
- Corrugated
Cell Shape
- Square
- Hexagonal
- Beneflex™
Proprietary honeycomb pattern known for its “flex” capabilities without heat (cold state) and scalable cell size from 1/8” cell to any size required in increments of 0.002” without tooling change.
Dimensions
- Min cell size: 1/8” (0.125”)
- Thickness range from 0.001” – 0.012”
- Core Depth from 0.25” – 10.00”
Key products
- Acoustic exhaust assemblies
- Metallic sandwich honeycomb panels
- Brazed honeycomb structures
- Missile control surfaces
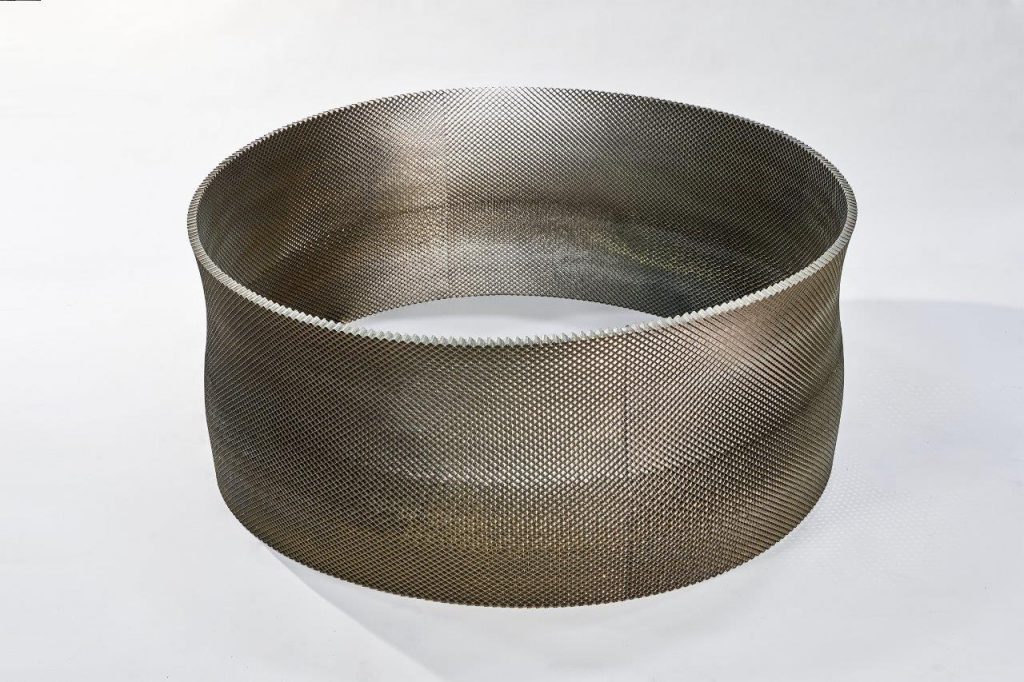
Engine Exhaust Front Plug Honeycomb Blanket
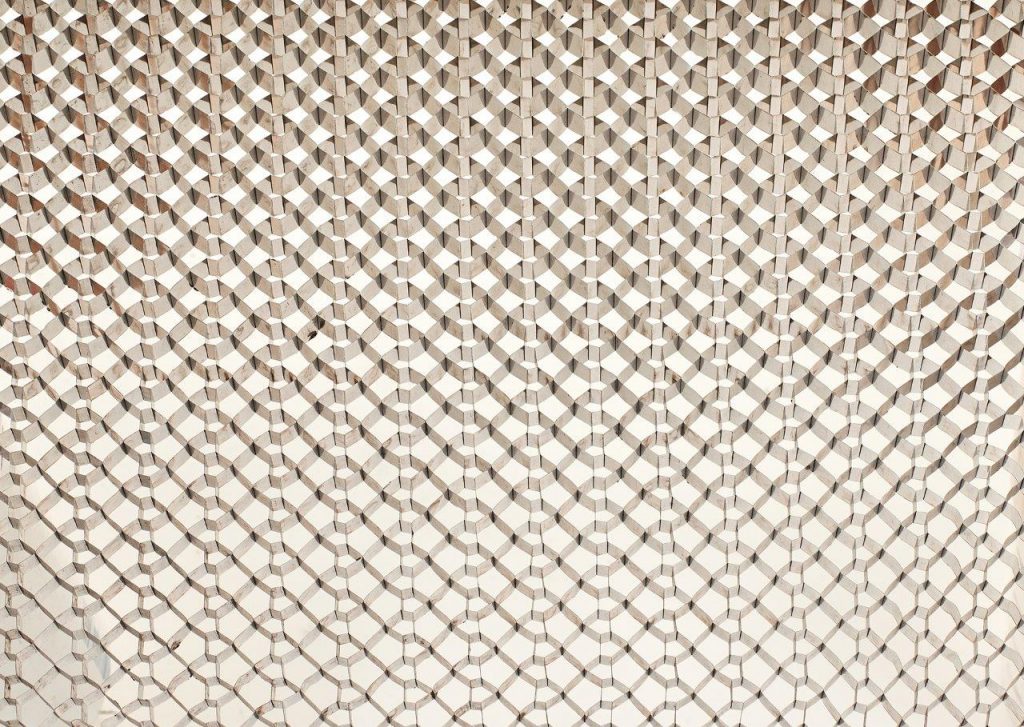
Beneflex™ Cell Titanium Honeycomb
filament winding
Filament winding is a fabrication technique mainly used for manufacturing cylinders or closed end structures such as pressure vessels or tanks. This process involves winding filaments under tension over a rotating mandrel. While filament wound structures are hollow, they are extremely lightweight with incomparable strength.
In many aerospace and defense applications, weight is as important as strength; products need to be as light as possible while retaining strength, and filament wound composite components provide the solution for these strength-to weight ratio challenges.
Filament wound structures may be applied to a wide range aerospace applications such as rocket motor casings, missile fuselage sections, and other structural composite bodies.
Magellan has been producing carbon fiber filament wound components for more than 25 years. This specialized niche capability offers light-weight components with exceptional strength and may replace metal parts that may be removed and re-installed. Magellan utilizes a phenolic-triazine resin system, which is in the category of high performance thermoset composites.
-
details
- On-site test lab, NDT testing that includes c-scan ultrasonic inspection capabilities
- Stress analysis and testing
- Climate controlled production environment
- 5-axis filament winder
- Average inner diameter tolerance +/- 0.001” as wound and cured.
- Checked with an air gauge that has an accuracy of +/-.0001”
- Capability to produce 2 ½” to 60” dia
- Capability to produce thicknesses up to 1”
-
key products
- Auxiliary power unit containment sleeves
Contacts
Tim Wise Program Manager T: +1 513 422 2751 ext. 24058 C: +1 513 849 0691 timothy.wise@magellan.aero For more information about Specialty Materials.
Andrew George Technical Sales Manager T: +1513 422 2751 ext. 24024 C: +1 937 336 2448 andrew.george@magellan.aero For more information about Specialty Materials.